Industries: Tips to increase productivity in your daily life!
Check out our important tips to help your industrial organization reach its maximum production. These actions listed below can bring several other improvements to your organization, such as the organizational climate and employee engagement.
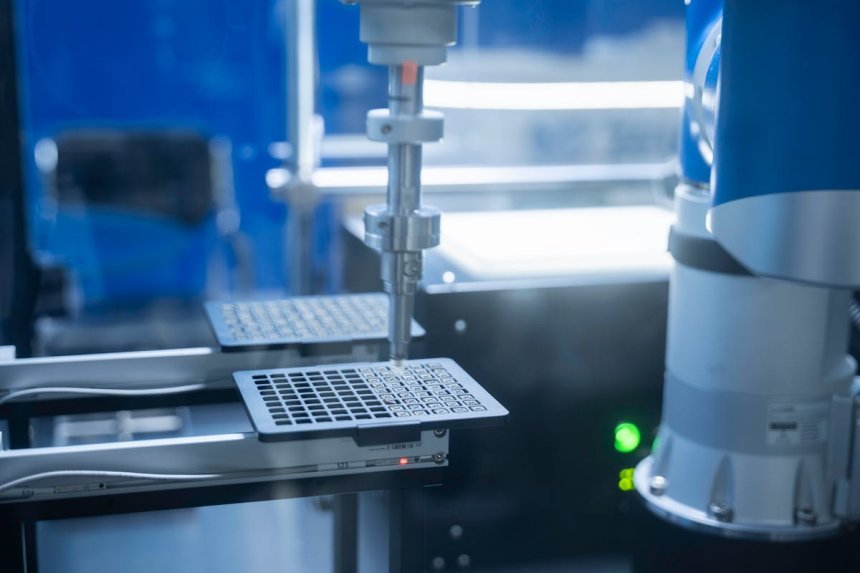
Productivity is essential for any type of business and this is no different for industries, as their success necessarily depends on generating profits that allow them to expand and consolidate their business.
Productivity may encounter obstacles to remain stable or even offer the growth initially expected. What can be done to ensure that it is not affected and, on the contrary, shows maximization and development?
We have put together some essential tips for you that could be the push your industrial unit needs to achieve the desired productivity. Check them out below!
How to increase productivity in industries?
Check out our important tips to help your industrial organization reach its maximum production. These actions listed below can bring several other improvements to your organization, such as the organizational climate and employee engagement.
Check out what they are and be sure to put them into practice to increase productivity!
1. Establish a goal policy
An organization that uses target policies tends to increase productivity, as employees become more engaged and have a better understanding of their goals and how to achieve them.
Industries must implement this type of policy. It is necessary to study the possibilities beforehand so that these goals are real and truly achievable.
They must be possible to achieve and not an exaggerated number that prevents the employee from complying with them, which can generate the opposite effect, corresponding to a lack of interest in the activities that will naturally hinder the company's production.
2. Automate processes
Automation is a natural part of industrial companies. This can be seen, for example, in the machinery used, which uses various technologies that allow production to be increased and the number of employees to be limited.
It is important to consider the possibilities of adopting automated systems not only for the factory environment, but for all sectors of the industry. These include, for example, the human resources department, the financial sector and the accounting sector.
With tools that automate bureaucratic procedures, employees can focus their attention on other points that really require it and that can bring more profitability to the organization.
. Put the feedback policy into practice
The feedback policy consists of adopting procedures based on dialogue and evaluation between the parties to a contract. In this case, both the employer and the employee exchange information regarding their impressions of each other within the work environment.
In relation to the employee, the manager can evaluate his/her production, attendance, proactivity employed in activities, the quality of these tasks and other points. The employee can share what he/she thinks about the company's environment, its internal policies and the opportunities offered.
While the employee can express his opinions on ways to better develop his activities within this industrial entity and how this organization can improve in some aspects, the manager can share indications on how the employee can grow internally and improve his actions.
4. Offer internal training programs
Internal training involves offering opportunities for intellectual and technical development in relation to activities. It is fully applicable to industries in general, in relation to all sectors.
To put this training into practice, the company invests in various courses that can be illustrated by lectures, seminars or even MBAs, undergraduate and postgraduate courses. The organization then agrees to cover at least part of the costs of the courses.
The costs of these costs should be seen as an investment made by the company. This is because trained employees tend to put into practice the knowledge they have acquired in their daily work activities.
Shows himself capable of presenting new ideas and suggestions that may be essential to the productivity of the industrial organization.
A trained employee tends to be more engaged in their activities from the moment they notice their value from the company that invests in their knowledge.
5. Job and salary plans
Another point that should not be ignored by industrial companies is the development and implementation of a job and salary plan. These plans are nothing more than roadmaps that show employees how they can grow within the organization.
This way, he knows what is necessary for him to achieve his professional goals, as well as the requirements outlined by the company as relevant to it in relation to an employee.
It is important to note that job and salary plans can help industry productivity as long as they are democratic. When a company implements them, it demonstrates that it takes into account the same requirements for all employees and that its choices are not biased. Meritocracy can then develop in a democratic environment in which everyone starts from the same point of view.
6. Perform constant maintenance on machinery
The machinery in the factory where the industry carries out its production is as essential as the employees who provide services to the organization. It is important that they are periodically evaluated and that maintenance is carried out.
This maintenance can prevent major problems that could result in the suspension of factory activities due to the need to repair machinery essential to production.
Another point that helps companies in relation to machinery and its useful life and, consequently, productivity, is ensuring that the employees who handle it have full knowledge of how it works and have been trained.
7. Develop an internal working hours policy
Employee attendance is essential to the productivity of a company, whether it is industrial or not. They are the ones who ensure the daily development of work activities that translate into production. Often, a lack of interest in tasks can affect the attendance of these employees.
The number of hours worked overtime directly affects the company, as it translates into additional payments at the end of the month, with different percentages. In this case, defining when overtime is necessary or not can be crucial.
These two points can be covered by an internal overtime policy. It can demonstrate, for example, when overtime is necessary and can define programs such as attendance bonuses to improve employees' attendance at work.
Share
What's Your Reaction?
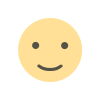
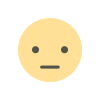
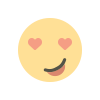
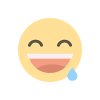
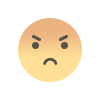
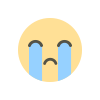
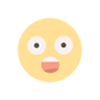