AI and OT-IT: Combining IT and Factory for Industry 5.0
Industrial evolution has always been marked by technological leaps that redefine production and competitiveness. While Industry 4.0 introduced automation and the Internet of Things (IoT) to the manufacturing landscape, we are now witnessing the birth of Industry 5.0 – a revolution that goes beyond pure automation, integrating human collaboration, IoT and, crucially, Artificial Intelligence to create truly intelligent production environments.
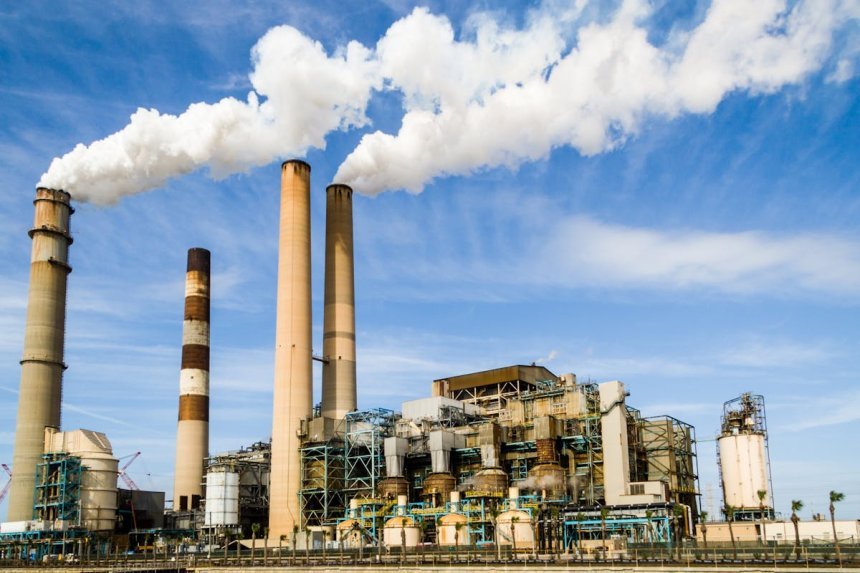
Industrial evolution has always been marked by technological leaps that redefine production and competitiveness. While Industry 4.0 introduced automation and the Internet of Things (IoT) to the manufacturing landscape, we are now witnessing the birth of Industry 5.0 – a revolution that goes beyond pure automation, integrating human collaboration, IoT and, crucially, Artificial Intelligence to create truly intelligent production environments.
From segregation to convergence: bridging two worlds
Historically, the industrial universe has operated with a clear division: on one side, Operational Technology (OT) controlling equipment, factory floor processes and SCADA systems; on the other, Information Technology (IT) managing servers, corporate networks and business applications. This separation, which made sense for decades, has now become a significant obstacle for companies seeking to effectively implement Artificial Intelligence in their industrial processes.
OT-IT convergence represents the breaking of this historical barrier, creating a unified environment where data from machines, sensors and shop floor systems flows directly into advanced analytics and AI platforms, enabling real-time decisions and insights impossible to obtain in siloed environments.
Pillars of Industry 5.0: far beyond automation
Industry 5.0 differs from its predecessor not only in its technological intensification, but also in the way it places human-machine collaboration at the heart of its strategy. This new industrial phase depends critically on three pillars:
- Expanded Industrial IoT : Advanced sensors capturing data from virtually every aspect of the production process, creating complete digital twins.
- Distributed Artificial Intelligence : Machine learning and deep learning algorithms operating both at the edge (close to machines) and in local industrial data centers, processing huge volumes of data in real time.
- Human-machine collaboration : Intuitive interfaces and assisted decision systems that amplify human capabilities rather than simply replacing them.
For this vision to come to fruition, the underlying infrastructure needs to be robust, reliable and integrated – a significant challenge for most industries.
Real challenges in OT-IT unification
The journey to integrate OT and IT faces technical and organizational hurdles that need to be overcome:
Different languages
Industrial systems often use proprietary protocols such as Modbus, Profinet, and OPC UA, while enterprise IT operates with TCP/IP, REST APIs, and web protocols. Making these worlds talk to each other requires dedicated gateways and translators.
Real-time requirements
While enterprise applications can tolerate a few milliseconds of latency, industrial processes operate in microseconds. A unified infrastructure needs to ensure deterministic and predictable performance, especially for control applications.
Expanded Cybersecurity
Security in OT environments has traditionally been based on physical isolation (“air gap”). Interconnection with IT exposes previously isolated systems to cyber risks, requiring a completely rethought security approach.
Data governance
For AI systems, data dependability and quality are essential. In industrial environments, data can be affected by electromagnetic interference, vibrations, and harsh conditions, creating additional challenges for accurate analysis.
Case studies: AI transforming industry through convergence
To illustrate the potential of OT-IT convergence for AI implementations, consider how integration can impact critical areas:
Advanced predictive maintenance
Integrating vibration, temperature, energy consumption and historical operating data through a unified infrastructure can feed AI algorithms that can detect degradation patterns long before failures occur. A company that implements this approach can potentially reduce unscheduled downtime by up to 45%, with a direct impact on productivity.
Computer vision-based quality control
High-resolution cameras on the factory floor, connected to edge computing systems, can feed deep learning algorithms to detect defects that are invisible to the human eye. The low latency provided by a local infrastructure allows for real-time rejection of defective parts without interrupting the production flow.
Smart energy optimization
Energy consumption sensors distributed throughout the manufacturing plant, integrated with control and analysis systems, allow AI algorithms to identify inefficient consumption patterns and make automatic adjustments to operating parameters, It has the potential to significantly lower energy use.
Infrastructure as the foundation of convergence
For OT-IT convergence and industrial AI applications to be successful, the underlying infrastructure needs to meet stringent requirements:
Robust industrial networks
Industrial Ethernet networks with redundancy, real-time determinism and resistance to adverse conditions (temperature, humidity, vibration) are essential. Technologies such as Time-Sensitive Networking (TSN) allow latency guarantees even in shared networks.
Specialized cabling
Industrial environments require cabling with superior electromagnetic interference protection, chemical resistance and mechanical resistance. The quality of the physical medium is often overlooked, but it directly impacts the reliability of the entire system.
Industrial edge and fog computing
The need for local processing with very low latency leads to the implementation of edge computing infrastructures directly on the factory floor, usually in industrial cabinets with adequate protection against dust and humidity.
Industrial data centers
Unlike traditional corporate data centers, industrial data centers must operate in much harsher conditions, requiring cooling, power and physical protection solutions specific to the manufacturing environment.
Share
What's Your Reaction?
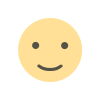
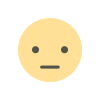
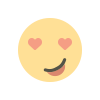
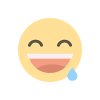
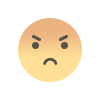
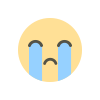
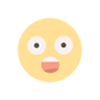